碳基臭氧催化劑,高效凈化,環保先鋒
- 簡要說明 :
- 文件版本 :
- 文件類型 :
一、背景與需求分析
臭氧高級氧化技術在水處理中扮演著重要角色,它通過產生強氧化性的羥基自由基來分解水中的有機污染物。然而,單獨使用臭氧時,其氧化能力受到限制,因為臭氧的直接反應速率較慢,且臭氧在水中的溶解度和穩定性不高。因此,引入非均相臭氧催化劑變得十分必要。這些催化劑能夠提高臭氧的分解效率,從而增強氧化過程。
非均相臭氧催化劑是指在不同相態中工作的催化劑,它們可以是固體、液體或氣體。在處理臭氧催化反應時,不同載體的催化劑具有各自的優缺點:
1. 金屬氧化物基催化劑:這類催化劑通常具有較高的催化活性和穩定性,但可能面臨成本較高和對環境敏感的問題。
2. 分子篩基催化劑:分子篩具有良好的熱穩定性和選擇性,但其合成成本較高,且在某些條件下可能失活。
3. 碳基催化劑:碳基催化劑,尤其是碳納米管和石墨烯等碳材料,具有以下優勢:
- 高比表面積:提供更多的活性位點,增強催化效率。
- 良好的化學穩定性:在多種化學環境下保持穩定,不易被腐蝕。
- 可調節的孔結構:通過改變碳材料的孔徑和分布,可以優化催化劑的性能。
- 環境友好:碳材料來源廣泛,制備過程相對環保。
- 可回收性:碳基催化劑通常易于回收再利用,減少資源浪費。
綜上,以碳基材料作為載體的非均相臭氧催化劑具有顯著的優勢。碳基材料如活性炭、碳納米管和石墨烯等,因其獨特的物理化學性質,如高比表面積、良好的導電性和化學穩定性,使得它們成為理想的催化劑載體。這些碳基載體能夠有效地吸附水中的有機污染物,并促進臭氧分子的分解,生成更多的羥基自由基。
二、碳基臭氧催化劑介紹
科力邇碳基臭氧催化劑(KHC-PC1001)
碳基材料廣泛存在于自然界中,大多通過煤、生物質等燃料熱解產生。在煤炭或生物質熱解過程中揮發分的釋放導致其內含大量孔隙結構,燃料中包含的大分子經過一次反應斷鍵形成多種中間產物,這些中間產物經過二次反應生成最終產物。碳基材料表面一般含有豐富的含氧官能團,同金屬基催化材料相比,碳基催化材料成本相對較低,具有較好比表面積、發達的孔隙結構,具有優良的吸附能力。同時,其發達的孔隙結構和高比表面積能夠為活性催化組分的負載提供空間和表面支撐。
科力邇選用碘值1100以上,比表面積1400m2/g的活性炭為基質制備出一種高活性的非均相臭氧催化劑——KHC-PC1001,其微觀結構如下圖所示。其具有的高比表面積為催化反應提供了更多的活性位點,在多種化學環境下都表現出良好的穩定性,這使得該型碳基臭氧催化劑在酸、堿和有機溶劑中都能保持較好的催化性能。碳基臭氧催化劑還具有優異的電子傳輸能力,這有助于加速催化反應中的電子轉移過程,同時碳基臭氧催化劑毒性較低,且材料來源廣泛,易于回收利用,符合綠色化學和可持續發展的要求。
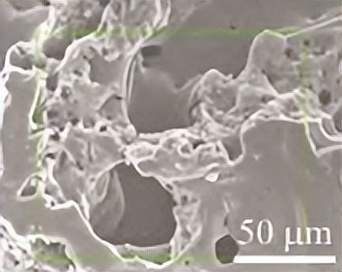
圖.碳基質微觀結構
2.技術優勢
碳基臭氧催化劑的制備過程主要是通過雜原子摻雜、表面改性和缺陷工程使碳基質功能化。通過碳前體原位摻雜以化學方法將外來金屬原子引入到碳骨架中,使原始碳的sp2電子構型發生改變,使之具有更加豐富的自由流動電子,碳材料邊緣缺陷又能夠介導電子,提升臭氧氧化體系中羥基自由基的產生效率。
多金屬雜原子共摻雜
金屬-雜原子共摻雜碳材料(具有更高的穩定性及催化活性。碳材料上引入雜原子有助于金屬物種在碳材料上的錨定,同時,金屬物質與引入的雜原子之間可能存在協同效應,進一步加強催化能力。過渡金屬能夠與碳基中不穩定的 C 形成 M-C 鍵,激活O3產生自由基。同時因為過渡金屬的負載能夠提高碳基的石墨化程度,有利于電子轉移增強催化劑性能。在實際工程應用過程中,摻雜單一金屬的一元催化劑無法表現出理想的催化能力,而多元催化劑能夠發揮“1+1>2”的催化效果,科力邇的研究人員利用多種金屬不同的-SA位點共存的優勢,通過配對和/或遠程耦合來改變彼此的協調環境,從而改變電子結構,以提高催化性能。
科力邇的研發人員將密度泛函理論應用到碳基多元金屬原子催化劑的篩選,構建了一系列 AC-M(M=Cu、V、W、Mo、Fe、Zn、Co)結構,并測定其單位臭氧COD絕對去除量,有針對性的篩選出潛在的臭氧催化劑(|ΔGH*| 值接近 0 eV)。如下圖2 介紹了其中一種鈷鎳雙原子催化劑的制備過程,Ni 基催化劑對 C-C、C-O 和 C-H 鍵的裂解均具有較高的活性,Co 同樣也對 C-C 鍵的斷裂有活性。
通過調整不同比例的鈷鎳雙金屬比例,得到了最高的雙位點密度,所制備的鈷鎳雙原子催化劑表現出完全的雙原子結構并獲得優異的臭氧催化活性。Ni原子的引入改變了活性中心的電子構型并降低Co的 d 帶中心,O-O 鍵在 Co-Ni 原子對位點上的斷裂要容易,表明Ni和 Co 之間存在的協同效應對催化活性起到了正向的影響,同時也提高了非均相催化劑對碳沉積抵抗能力。通過DFT 計算,鈷鎳雙原子催化劑能顯著降低臭氧氧化中間體階躍的相對自由能,表明鈷鎳雙原子催化劑再弱堿性條件下具有優異的臭氧催化活性。
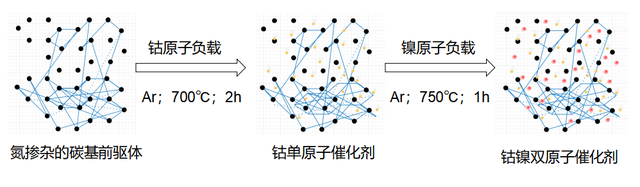
圖2.鈷鎳雙原子催化劑的制備過程
多金屬合金催化劑之間的協同效應,不同種金屬的摻雜原則如下:
1)添加的多種金屬能提高催化劑的穩定性,減少納米粒子團聚現象,達到提高催化活性的目的;
2)添加的多種金屬能改變金屬的電子特性和微觀結構,使其提高了參與催化反應中間體的穩定性,從而提高催化活性;
3)多金屬合金催化劑中不同金屬之間電子的相互作用以及幾何效應,能對納米粒子起到了修飾的作用,從而提高催化活性。
穩定性好
碳基材料本身具有含有豐富的氮原子,N與碳的結構相似,因此很容易作為雜原子進行摻雜,在催化領域為研究新型催化劑提供了新的可能性。氮為反應物的最佳吸附提供了基礎位置,同時具有良好的電子密度,由于氮的存在,使得活性相具有更好分散性和使得電子性質發生變化,因此可以提高催化性能。同時氮原子可以有效地錨定和穩固單金屬原子,從而避免金屬原子遭受到遷移和聚集,能夠穩住高流動性金屬原子,在熱解過程中作為氮源形成強金屬-氮配位鍵,極大地提高了材料的熱穩定性和化學穩定性。
由于金屬-氮配位相互作用更強,可以在高溫下穩定金屬-氮配位鍵,因此科力邇的研究人員在金屬負載的過程中優選氮含量多的有機連接體(例如戊二醛286、乙二醛;環氧氯丙烷等其中的一種或多種),氨基與雙醛以席夫堿的形式形成羧酰胺鍵,極大程度的改善了碳基材料的機械性能和熱穩定性。同時通過有機交聯劑的修飾為碳基體螯合金屬離子提供更多的活性位點,增加了負載金屬催化劑對金屬的負載能力。金屬-氮邊界處具有復雜的絡合結構,這些結構有助于金屬成分與碳結構之間的 電荷傳輸,使得碳材料表面相互作用的局部區域具有更加密集的電子狀態,從而具有更高的催化活性。形成的 C@N 鍵提高了對金屬離子螯合效果,使得碳基臭氧催化劑的金屬浸出風險大大降低,保證了碳基臭氧催化劑的安全性以及使用壽命。
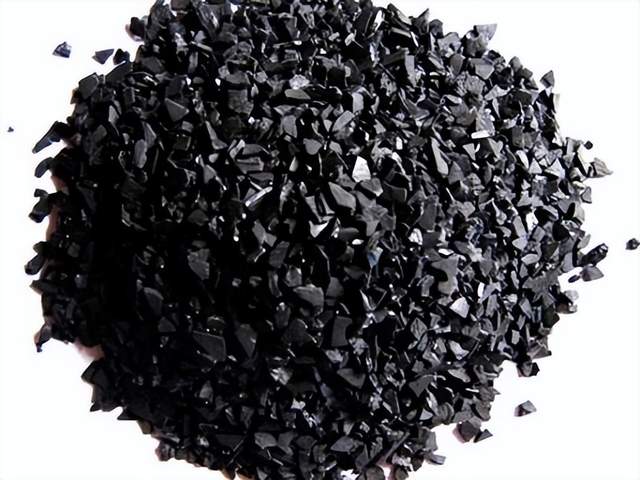
圖.KHC-PC1001催化劑
成孔工藝
孔隙率是影響催化劑具有較高催化活性的一個至關重要的因素。高孔隙率和高表面積使反應分子易于進入活性物質??屏兊腒HC-PC1001型碳基臭氧催化劑使用的碳基體便具有多孔結后,其比表面積可超過1200 m2/g。為了避免金屬離子的摻雜導致碳基體部分微孔堵塞,減小成品的比表面積,科力邇的研究人員采用了多種思路來解決這一難題。
其一,便是單次負載單一負載的多次燒結工藝,該工藝在保證金屬均勻負載,最大程度增加氧化活性位點數量的同時,避免了金屬聚集結團堵塞碳基體微孔的風險。
其二,便是在金屬負載的過程中添加一定比例的水溶性致孔劑,例如(PEG,PVP,PVA 等。)水溶性致孔劑在催化劑材料制備中的工作原理主要是通過其在混合過程中的均勻分布和后續的去除,形成具有特定孔結構的催化劑,提高其催化效率。其在催化劑材料的制備過程中主要通過以下幾個步驟發揮作用:
1)溶解與混合:水溶性致孔劑通常在水相中溶解,與其他組成材料(如金屬鹽、載體等)充分混合,形成均勻的膠體或溶液。
2)聚合與成型:在適當的條件下,這些混合物會通過加熱、冷卻、或者化學反應等方式形成固體基體。在這一過程中,水溶性致孔劑均勻分布在固體基體中。
3)去除致孔劑:在后續的處理過程中,例如干燥或煅燒,水溶性致孔劑會被去除。由于其水溶性,可以通過簡單的水洗或高溫煅燒使其揮發,從而在催化劑中形成孔隙。
4)孔結構的形成:致孔劑的去除留下一定的空間,形成多孔結構。這些孔隙能夠提供較大的比表面積,有助于提高催化劑的活性和選擇性。
5)催化性能優化:通過調節水溶性致孔劑的類型、濃度以及去除的方式,可以控制最終催化劑的孔徑、孔容和分布,從而優化其催化性能。
其三,犧牲模版金屬造孔法,利用可溶性的金屬作為模版,在催化劑煅燒過程被去除被包裹在待制備材料周圍,從而留下空腔或孔隙結構,例如在碳基臭氧催化劑的制備過程中,Co2+、Ni2+、Fe2+中的一種或幾種金屬分別隨著Zn+一同負載在碳基體上,金屬離子可以和連接體2-甲基咪唑進行配位并均勻分布于ZIF框架中,從而可以產生多金屬ZIF。目標金屬位點由2-甲基咪唑連接體和鋅原子在空間上隔開,導致兩者之間的空間距離變得更長。因此,在高溫煅燒過程中ZIF骨架中的鋅被蒸發掉后可以充當成孔劑, 從而產生大量的開放通道。
表.椰殼炭與KHC-PC1001不同孔隙比表面積貢獻
通過以上三種方法,科力邇制備出的碳基臭氧催化劑比表面積超過1286 m2/g,在原有的碳基體基礎上有所提升,通過碳基體與該型碳基臭氧催化劑的掃描電鏡圖也可看出,未經修飾的碳基體孔壁光滑,而該型號碳基臭氧催化劑的表面存在大量金屬氧化物晶體,這些金屬晶體分布均勻,對催化劑的比表面積,吸附性能以及空隙分布均有一定的提升
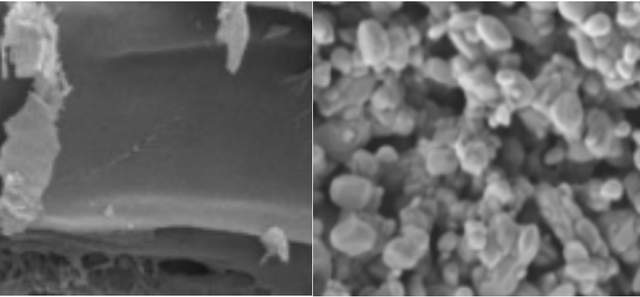
圖.碳基體與KHC-PC1001的掃描電鏡圖(10000X)
(4)原位多段煅燒-退化工藝
高溫煅燒過程對金屬負載型催化劑的作用至關重要,它直接影響催化劑的物理化學性質和催化性能。煅燒過程可以去除雜質和形成晶體結構:煅燒可以去除原料中的水分和揮發性成分,去除毒素并防止金屬聚集,從而恢復催化劑的活性。同時通過高溫處理使無定形相轉變為晶體相,改善催化劑的熱穩定性、物理化學性能,并且增加其固定碳含量,從而滿足產品要求。同時煅燒可以改變催化劑表面的酸性、比表面積等性質。煅燒還有助于金屬與載體之間的相互作用,從而提高催化劑的整體性能。煅燒溫度、煅燒時間、升溫速度等是影響催化劑性能的關鍵因素。
1)煅燒溫度:煅燒溫度對催化劑的比表面積、孔隙結構和表面活性組分的分散度有顯著影響。對于KHC-PC1001催化劑,700℃的煅燒溫度能夠獲得最佳的選擇性臭氧催化活性,因為在這一溫度下,催化劑具有最大的比表面積和發達的孔隙結構。而當煅燒溫度過高(如1000℃以上)時,催化劑表面會出現燒結現象,導致比表面積減少,不利于催化反應的進行。
2)煅燒時間:煅燒時間同樣影響催化劑的物理化學性質。不足的煅燒時間可能導致催化劑前驅體未完全分解,活性組分無法充分形成或分散,從而影響催化劑的活性。而煅燒時間過長則可能導致催化劑燒結、比表面積減小、孔徑塌陷等不利變化,降低催化劑的性能。例如,KHC-PC1001催化劑在700℃煅燒8小時后,表現出良好性能。
3)升溫速度:升溫速率的控制也對催化劑的性能有影響。過快的升溫可能導致催化劑前驅體在達到最佳煅燒溫度前未完全分解,而過慢的升溫速率則會延長整個煅燒過程的時間,影響催化劑的最終性能。
綜上所述,煅燒過程的優化對于制備高性能的金屬負載型催化劑至關重要。通過控制煅燒溫度、時間和升溫速度,可以有效地調節催化劑的物理化學性質,從而提高其催化活性和穩定性。這些因素的優化需要根據具體的催化劑體系和應用需求來進行,科力邇的研究人員采取正交試驗的方式,篩選出的最優的燒結條件,以確保催化劑在實際應用中達到最佳性能。
3、產品參數
表.KHC-PC1001型碳基臭氧催化劑和椰殼活性炭性能對比
產品優勢
該型碳基臭氧催化劑的優勢主要包括以下幾點:
1)高比表面積:具有非常高的比表面積(約1300m2/g),這使得它能夠提供大量的活性位點,提高催化效率。
2)多孔結構:多孔結構有助于提高活性組分的分散性,減少催化劑顆粒的團聚現象,從而提升催化活性和穩定性。
3)化學穩定性:材料具有良好的化學穩定性,可以在多種化學反應條件下保持結構不變,保證催化劑的長期使用。
4)機械強度:通常具有較好的機械強度,這有助于在反應過程中保持催化劑的完整性,減少磨損和破碎,年磨損率<2%。
5)可調節的孔徑分布:通過不同的制備方法和后處理技術,可以調節孔徑分布,以適應不同大小催化劑顆粒的需求。
6)易于回收和再生:在使用后可以通過簡單的物理或化學方法進行回收和再生,便于重復使用,減少環境污染。
8)應用廣泛:它們可以用于處理各種類型的工業廢水,包括但不限于紡織、造紙、電子、制藥和食品加工等行業,催化效果好、材料來源廣泛,容易再生,環境友好,具有廣闊的應用前景。
應用領域與案例分析
1)含油污水(油田采出水,壓濾返排液、罐區切水、乳化酸性水)
具有優良的吸附性能,可吸附廢水中的分散油、乳化油和溶解油。再利用其優越的臭氧催化性能可快速分解富集在催化劑表面的有機物,實現污水廠含油廢水的深度處理。例如科力邇利用碳基臭氧催化劑處理新疆某石化含油廢水,該含油廢水先經隔油、氣浮和生物處理,再用碳基臭氧催化劑進行深度處理。再臭氧投加量為100 ppm時,原水COD為180 mg/L,出水COD僅為23 mg/L,COD去除率超過90%;進水含油量35 ppm,出水含油量2.3 ppm。除此之外廢水的含酚量從0.1 mg/L降至0.005 mg/L,含氰量從0.19 mg/L降至0.048 mg/L,COD從85 mg/L 降至18 mg/L。處理前后的水樣圖如下圖所示。
碳基臭氧催化劑對油的吸附容量有限(一般為30~80 mg/g)),通常用作含油廢水多級處理的最后一級處理,出水含油質量濃度可降至0.1~0.2 mg/L ,以達到深度凈化的目的。
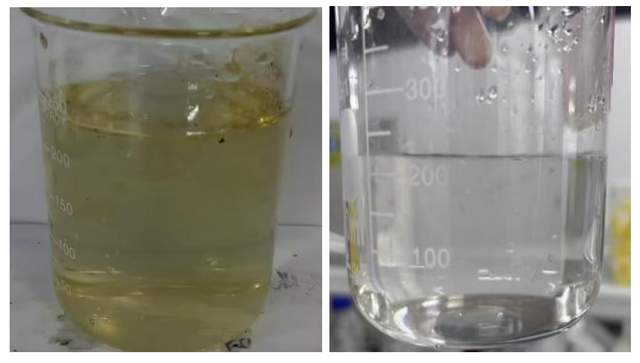
圖.KHC-PC1001處理新疆某石化廢水的效果對比(左進水,右出水)
2)垃圾滲濾液
垃圾滲濾液是在垃圾堆放和填埋過程中,由于微生物自身降解、雨雪沖刷等產生的黑棕色液體,具有有機物含量多、毒性大、異味大、地區差異大、難降解等特點,是一類成分復雜,難以生化降解的廢水。科力邇科技公司針對垃圾滲濾液處理所研發的CDOF(Cyclonic Dissolved Ozone Flotation Unit)專利技術,裝置內填充80%的KHC-PC1001,其反應原理是臭氧通入水中產生具有強氧化性的·OH,將垃圾滲濾液中難降解的大分子有機物氧化為易降解的小分子有機物,甚至礦化為CO2和H2O。CDOF具有反應速率快,設備簡單、便于操作、無二次污染等優勢,在垃圾滲濾液處理領域具有廣泛前景。
科力邇全量化工藝處理浙江某垃圾填埋場老齡垃圾滲濾液,處理效果令人滿意,該工藝對垃圾滲濾液的COD去除率超過80%,臭氧投加比僅為1.2左右,水質指標改善較大,處理前后水樣對比明顯。經過氧化處理后的濃縮液再回到污水廠的生化池處理,避免了污染物在污水系統中循環導致污水系統持續惡化的局面。該工藝處理深圳某垃圾滲濾液效果同樣喜人,其處理前后對比如下圖所示,進水COD約1500mg/L,經KHC-PC1001臭氧催化氧化工藝,20min出水400mg/L,40 min出水江COD降至200mg/L一下,廢水B/C從0.22提升至0.37。同時,該技術不僅達到了全量化處理,還使污水廠運行更加穩定,也大幅降低了濃縮液處理成本。
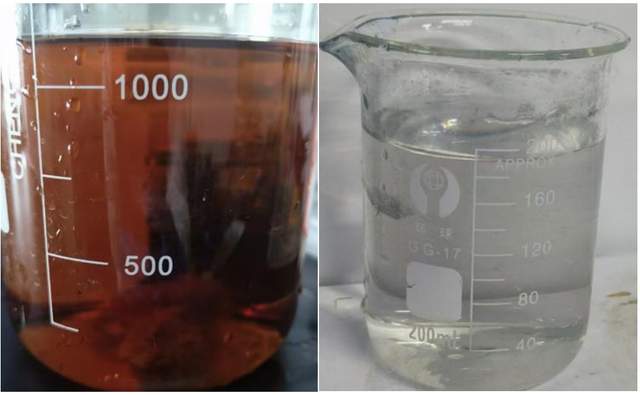
圖.KHC-PC1001處理浙江某垃圾滲濾液前后對比(原水;出水)

圖.KHC-PC1001處理深圳某垃圾滲濾液前后對比(原水;20min出水;40min出水)
3)染料廢水
染料廢水成分復雜、水質變化大、色度深、濃度大,處理困難。處理方法主要有氧化、吸附、膜分離、絮凝、生物降解等。這些方法各有優缺點,其中活性炭能有效地去除廢水的色度和COD?;钚蕴刻幚砣玖蠌U水在國內外都有研究,但大多數是和其它工藝耦合,碳基臭氧催化劑對染料廢水有良好的脫色效果。染料廢水的脫色率隨溫度的升高而增加,而pH值對染料廢水的脫色效果沒有太大的影響。在最佳氧化工藝條件下,酸性品紅、堿性品紅廢水的脫色率均>97%,出水的色度稀釋倍數≤50倍,COD<50 mg/L,達到國家一級排放標準。
科力邇使用KHC-PC1001臭氧氧化工藝處理某工廠混合染料廢水以及亞甲基藍廢水,其效果圖如下圖所示,混合染料廢水中包括亞甲基藍、甲基紅、甲基橙、羅丹明等多種染料,色度>10000,TOC超過2000mg/L,經臭氧催化氧化處理后,臭氧投加量為200ppm時,脫色率超過99.9%,礦化率超過45%;亞甲基藍廢水色度>1000,TOC>500mg/L,在臭氧投加量為100ppm時,脫色率超過99.9%,礦化率超過47%。
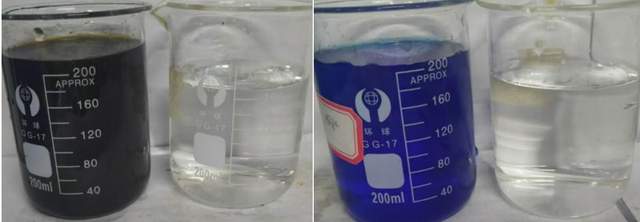
圖.KHC-PC1001處理混合偶氮染料廢水、亞甲基藍染料廢水效果圖
科力邇碳基臭氧催化劑,獨特的制備工藝,確保了催化劑表面擁有極高的活性位點密度,從而顯著提升了催化效率。此外,科力邇還注重催化劑的穩定性與耐用性,通過特殊的表面處理與結構設計,有效延長了催化劑的使用壽命,降低了用戶的使用成本。
與市面上的其他臭氧催化劑相比,科力邇碳基臭氧催化劑展現出了顯著的優勢。在催化效率方面,科力邇產品能夠更快、更徹底地完成臭氧的生成與分解,為用戶帶來更高的生產效率與更優質的產品質量。在環保性能方面,科力邇催化劑在催化過程中幾乎不產生任何有害物質,真正實現了綠色、環保的生產理念。
綜上所述,科力邇碳基臭氧催化劑催化效率高、環保性能優秀,具有良好的應用前景。